
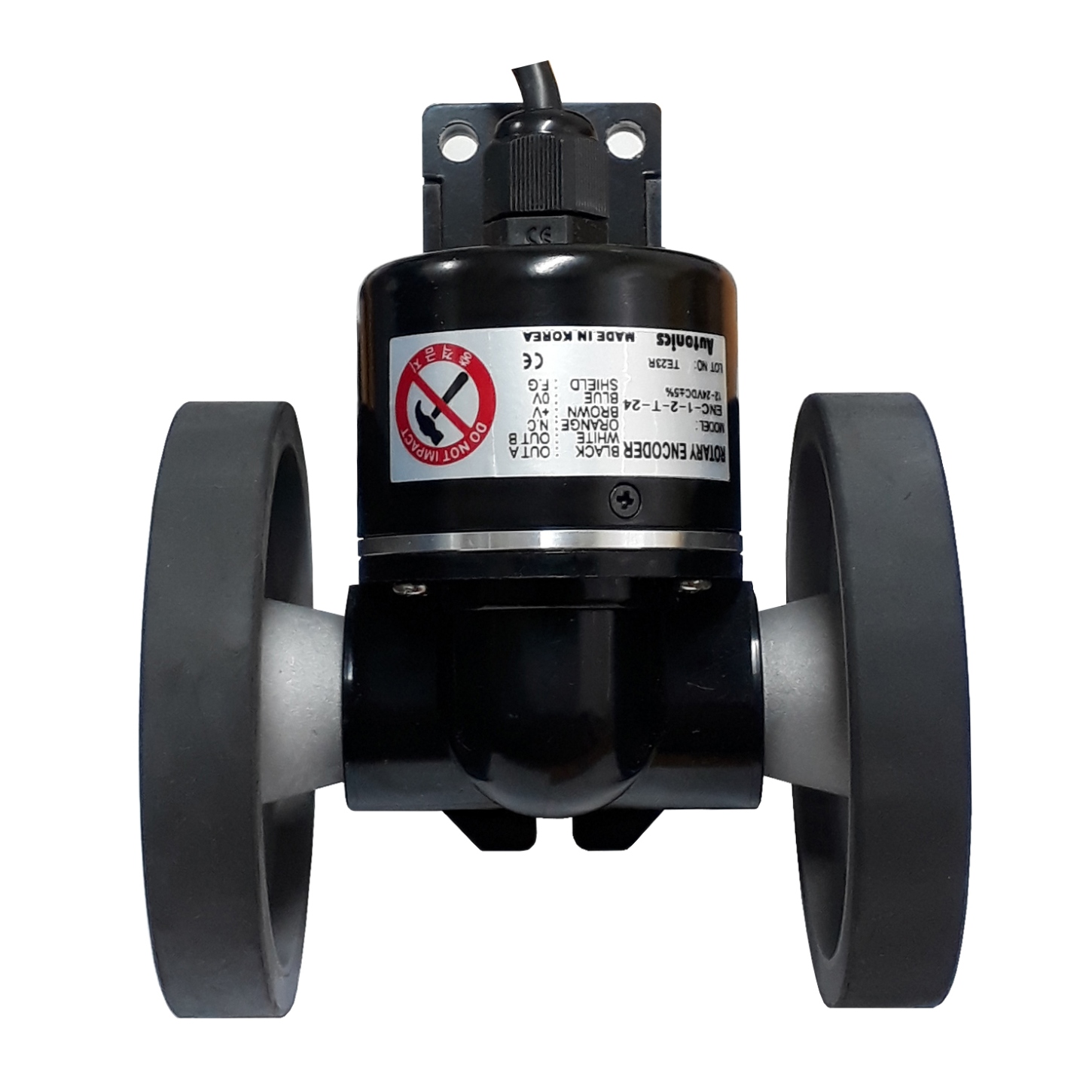
Controllers can compare each pair (“A” must be equal to inverted “/A”) to ensure that there is no error during the transmission.Īdditionally the transmission sensitivity is improved by transmitting the differential signals through a twisted pair cable. These signals are inverted “A”, “B” and “Z” signals. Some incremental encoders also have additional differential signals, called “/A”, “/B” and “/Z”. This can be used as an accurate reference point. Once every rotation, this Z signal is rising for typically 90°, on the exact same position.

By turning the encoder clockwise, the “A” pulse is rising 90° ahead of the “B” pulse, by turning the shaft counterclockwise, the “B” pulse is rising ahead of the “A” pulse.Īdditionally some incremental encoders output a “Z” signal. These 2 signals are set up with a 90° offset, which is required for the detection of the encoder’s rotation.
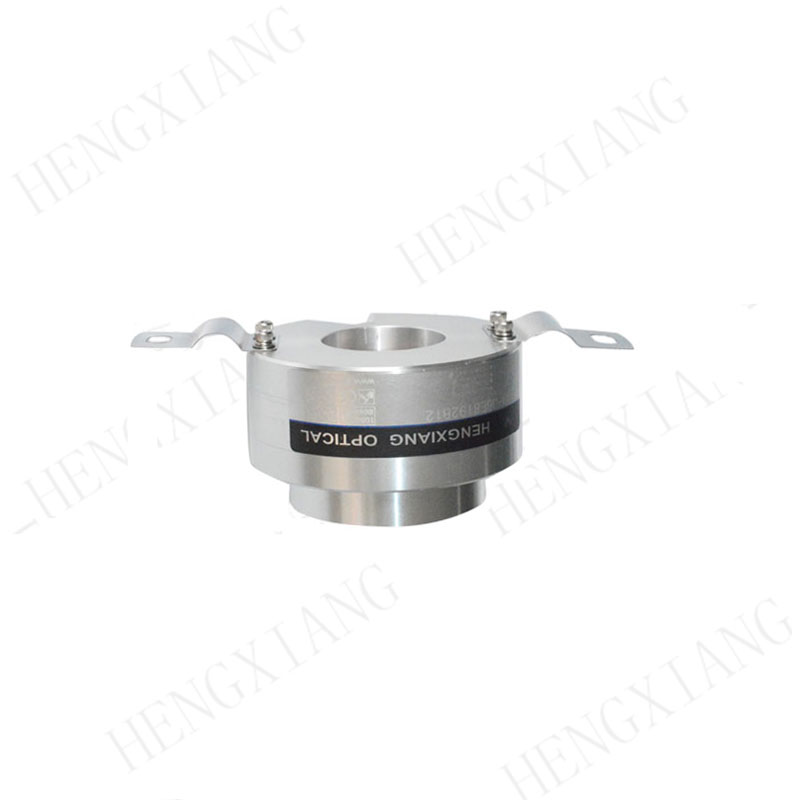
One sensor must be connected to one controller.Īn incremental encoder has at least 1 output signal “A” or typically 2 output signals, called “A” and “B”. Please refer to the table below for a simple example of a push-pull output.Incremental rotary encoders provide a serial output signal on a single transmission line. So even without connected to a load, the Encoder Output is referenced to the supply voltage. In the off state it will supply a path to ground and in the on state it will supply Vcc. With Totem-pole, the output contains back-to-back transistor. Please refer to the table below for a simple example of an open collector.Ī push-pull output is a combination of a line driver and an open collector. For proper operation, a sourcing input is required. When in the off state, an open collector will float. In the on state, an open collector will supply a path to ground. Please refer to the table below for a simple example of a line driver.Īn open collector is a sinking output. Because of this, a sinking input is required for proper operation. In the off state, a line driver will float. When in the on state, a line driver will supply Vcc. An encoder (for industrial controls) is a special sensor that captures position information and relays that data to other devices. If you are working with an Industrial I/O Card, check the user manual for the best quadrature encoder type.Ī line driver is a sourcing output. The Push-Pull configuration does not float, it is always supplying Vcc or ground, which is why it will work best with a Multifunction DAQ card. SolutionFor most NI DAQ cards, a Push-Pull quadrature encoder is recommended since Multifunction DAQ card works best when it is constantly driven.
